Introduction
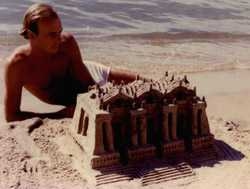
My name is Angus Wyman Macdonald. I am an architect, and this document is an introduction to my invention, the prefab & panelized am‑cor Ferrocement System.
I graduated from Yale University in 1964, Cum Laude, as a Saybrook ranking scholar, and from the Yale School of Architecture in 1967 with the AIA award for “excellence in the Study of Architecture”. From Yale, I went to New York City, and worked for Harrison & Abramovitz Architects. I gravitated towards warmer climes, working as an architect in Jamaica, West Indies, and began development of a comprehensive, low-cost construction system. I wished to unite my aspirations as a designer with the world-wide need for durable, energy efficient, and affordable shelter.
The Problem
I had always been interested in modular, mass produceable building systems. However, I was never happy with the tradeoffs I encountered over the years. While one particular building system was beautiful, it was not affordable. While another was affordable, it was not disaster resistant or suitable to below-ground construction, such as earth-berming/sheltering. Yet another was energy-efficient, but quite difficult to design and build, much less maintain. In frustration, I decided to look at the construction process holistically, and identified the following problems with standard construction:
- Fasteners are used to connect components; fasteners are the weak points, yet are used throughout.
- The usual method of making a stronger structure is to “throw more material at the problem”, rather than “use the properties of the material intelligently”.
- Much effort is repeated or unnecessary and money is wasted, because of constant focus on cheapest materials rather than coordination between each stage of construction.
- Basically, standard construction is 200-300 year old technology, patched with contemporary “band-aid solutions”, giving the appearance of modernity.
Prefabrication & Panelization
I knew there must be a way to deal with the problems of modern construction cheaply & efficiently. My experiences with various building systems showed panelization of the building shell to be the most effective way to:
- Prefab: Utilize the efficiency of industrial mass production techniques to control cost
- Provide the widest and most flexible vocabulary of forms to suit various sites and designs, and
- Allow ready transportation to, and easy assembly at, remote sites.
While panelized construction is compelling, normally the panels themselves have issues. Junctions are a problem, as it is complicated to obtain structural continuity using finished panels; furthermore, they are not aesthetically pleasing and have the stigma of being “cheap.” Joints can admit moisture and weather, and the strength of panelized building normally relies on fasteners. Merely fastened connections eventually fail, as they are only as strong as the material surrounding them.
Experience
I have designed for and personally built with various types of panels, and so have experienced their various characteristics:
- Mass produced wood framing
- Pre-cast concrete
- Bagasse board (made from sugar can stalks after the sugar has been pressed out)
- Steel frame with wooden infill walls, floors, and roof panels
- SIPS (structural insulated panel system) & ICF (insulated concrete forms)
- Modular removable steel formwork, to cast thin shell reinforced concrete building shells in situ
- Heavy timber & concrete block/masonry
While each of these systems has laudable strengths, each also has disqualifying shortcomings. In comparison, the panel type I invented, in response to my hands-on experiences setting up panel assembly lines, is based on ferrocement engineering. It is made of a galvanized light-gage cold rolled steel framework, coated on site with a thin continuous seamless highly reinforced, Ferrocement skin. By panelizing the building framework as a structural matrix for on site placement of a structural ferrocement coating, I combined the composite qualities of ferrocement with the opportunity for mass production of building structures.
The Solution
I patented this panel type in 1996 and called it the am‑cor System™. In this system, fasteners are used to hold the frame together during application of the Ferrocement skin. However, they are actually redundant: on hardening, the Ferrocement skin itself becomes the ultimate “fastener”, joining all frame parts together to form a composite unibody monoqocue shell, similar to a boat hull, automobile chassis, or airplane fuselage. By harnessing the inherent physical & chemical properties of steel and cement, I have been able to create a composite assembly that is completely modern and efficient in its use of materials.
Over time, I have improved the performance of the am-cor System through collaboration with builders, engineers, and cementologists, and by constructing many buildings for clients. Today, we are at a point where the qualities of this invention satisfy my building system wish-list:
- Conforms to international building codes for immediate application world-wide
- Mass produceable by regional fabricators (and so readily available world-wide at extremely low cost)
- Raw materials readily available world-wide
- Energy & labor efficient, especially during construction, and over the lifetime of the building
- Modern, renewable energy and service systems are easily integrated into the panelized structure
- Easily expanded, extended, and added onto
- Safe & secure, for affordable “fortified and ballistic resistant construction”
- Truly sustainable & resilient: Minimal use of recycled materials that last
- Extremely strong (high strength-to-weight ratio)
- Durable and resistant to all types of deterioration including rot , delamination, and rust
- Disaster resistant: flood, fire, hurricane, tornado, flood, earthquake
- Resistant to vermin, insects, termites
- Easily made hygienic, resistant to mold, mildew, fungus, bacteria
- Inexpensive & affordable
- Completely scalable: equally good for large and small projects
- Transportable (nestable & flat-packing)
- Easily assembled and enclosed by owners and local builder crews (fast learning-curve)
- Simplicity of construction & materials eliminates complicated details and redundant building practices
- Beautiful: with interiors and exteriors complimentary to regional traditional architectural styles
- And above all: workable in a way to fulfill the concepts and aspirations of the designer; truly universal, without design constraints of size, shape, texture, surface or appearance.
The Future
The am‑cor Unified Steel & Cement™ System has been used to make many building types, including residences, below-ground earth-sheletered/earth-bermed structures, community buildings, offices, restaurants & food service, agricultural industrial, schools and day care centers, hotels and casinos. In each case our Ferrocement engineering & formulas has proven to provide the optimum balance of construction speed, low cost, and building quality.
The success of the am-cor System in the USA and abroad is leading to a new structural paradigm. New ideas and methods will open up the potential for even greater strength and weather resistance, using even less material, at even lower cost.
It is my goal to follow this path: to make sustainable, resillient, energy-efficient, and permanent shelter affordable to all people.
To learn more about Angus W. Macdonald:
- Read his blog
- Find him on Facebook or LinkedIn
- Visit his architectural firm